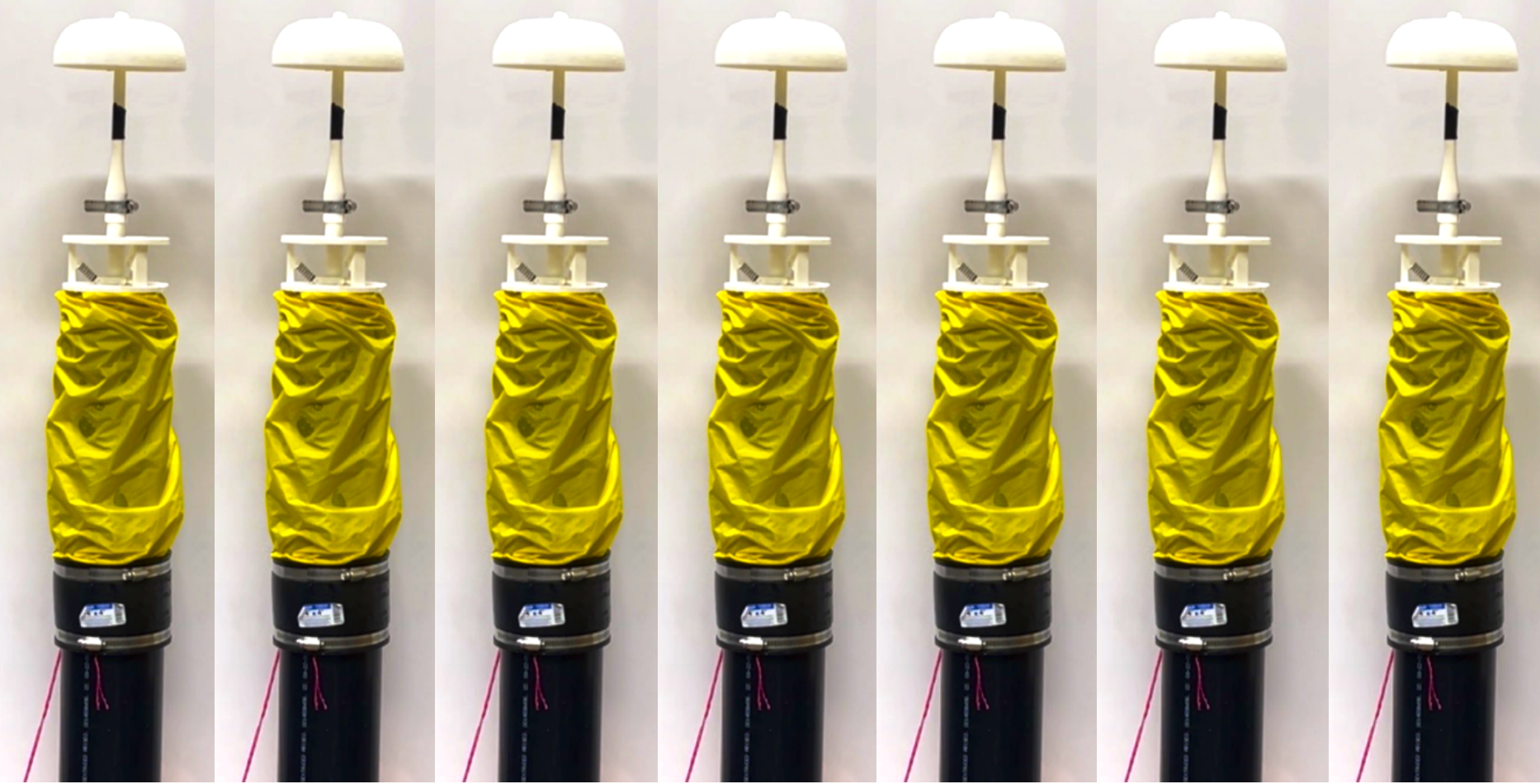
Failsafe Design for Gravity Energy Storage Systems in Idle Oil & Gas Wells
Skills:
fluid analysis
FMEA
mechanism design
prototype design and testing
project management
The Project
A mechanical failsafe for a gravity energy storage system.
Background
For my senior capstone, I had the privilege of collaborating with Renewell, a renewable energy storage start-up. The intermittent nature of wind and solar energy provides a hurdle to renewable sources. However, Renewell has developed a system that uses excess energy to raise a massive cylindrical weight inside inactive oil wells and then lowers the weight to release the stored energy to the grid when needed.
The Problem
When all goes well, the Renewell systems promise 132-gigawatt hours of stored
potential energy. However, if something goes wrong, a 30-ton weight could end up plummeting 30 m/s toward a toxic reservoir of pressurized oil industry residue.
Our job was to design a failsafe that could sense a falling weight and slow it down.
Our Solution
Our solution takes advantage of the packing fluid filling the well. We model the movement of this packing fluid in the annulus between the side of the weight and the wall of the well as fluid escaping through a piston.
Assuming the fluid is non-compressible, the fluid must be displaced as the weight moves down. Therefore, our solution creates a smaller region for this fluid to move through by narrowing the annular region.
Full Scale Model
Our failsafe design uses an expanding fabric airbag to achieve annulus reduction. The airbag is expanded by a chemical reaction of sodium azide, the same reaction used in car airbags. A bistable mechanism triggers the reaction at a predetermined fall speed based on a drag force felt by a drogue parachute.
1.
2.
3.
1. Failsafe in typical operating conditions, unactivated. 2. Failsafe activated by the trigger of bistable mechanism. 3. Labeled cross section of full-scale model.
Low Fidelity Prototypes
In the process of designing our failsafe system, we proposed several potential solutions and then conducted an FMEA to determine which solutions were the most promising. We created rapid prototypes of our top three ideas and ultimately chose to conduct more rigorous prototyping on our inflatable airbag solution.
Shown below are our low-fidelity prototypes that informed our decision to push forward with our airbag failsafe.
Test: Using a force gauge to test the required force needed to trigger the bistable mechanism.
Results: A consistent force is required, therefore we are able to tune the drag on the drogue parachute to trigger at a specific speed.
Test: Dropped weights with different annulus reductions down a clear acrylic tube and measured falling speed.
Results: Speed reduced in a quadratic relationship to annulus size. Even better than the predicted cubic relationship!
Test: Scraping ripstop nylon with nails to test its abrasion resistance.
Results: Zero tears > 1 mm. Promising abrasion resistance.
Full-System Prototype
We designed and built the below prototype in order to test our full failsafe system. Our weight prototype and test set-up involved plugged pipes, cut to length, of PVC and clear acrylic. We filled the PVC pipe section with steel BB pellets to mimic the weight. Inside the weight, a series of tubing connects the pneumatic airbag inflation system to a CO2 cartridge and regulator valve. When the drogue parachute senses freefall, the bi-stable mechanism releases the pressurized CO2 from the cartridge into the airbag.
The testing set-up: dropping our weight and attached failsafe down a water-filled clear acrylic tube.
Testing Videos
Weight falling without failsafe at 0.25 m/s.
Weight falling with triggered failsafe at 0.05 m/s.
Slow motion failsafe triggering. The drogue parachute senses the weight is in freefall and triggers the bistable mechanism, which releases compressed CO2 into the airbag. The airbag expands and slows the falling weight.
Future Work
The main next step for anyone continuing this project would be to complete the process of scaling our prototype to a full-size system. The speed reduction achievable in an actual well will be dependent on four main components: mass of the weight, weight length, annulus reduction length, and airbag pressure. We were only able to test one of these components in our prototype: the mass of the weight. Our team would further recommend more testing on the full multilayered airbag design to guarantee it can hold the required pressure. Our design relies heavily on the consistent behavior of a combination of fabrics, which we understand could be highly unstable. Currently, our team recommends layering ripstop nylon, kevlar, and then another layer of ripstop nylon for the airbag. More testing on the abrasion resistance and pressure limits of this airbag system is required. We would also recommend additional testing on the drogue parachute sensing mechanism to ensure it senses the appropriate drag force and deploys the airbag correctly.